Farmers have been making silage piles for years, but some practices have allowed huge storage losses. Silage exposed to oxygen deteriorates rapidly. Packing forces oxygen from the silage and limits porosity. Excluding oxygen is essential to produce good fermentation and well preserved silage. Without proper packing, spoilage can exceed 30 percent of the ensiled dry matter. This level of spoilage is unacceptable and unnecessary. To ensure proper packing, you need heavy tractor(s) and proper pile design and packing technique.
The following step-by-step technique produces an inexpensive and efficient storage option that can limit dry matter losses to 10 to 20 percent.
Site Location
Before you begin, consider these location variables:
Drainage
Select an elevated location which allows rain and snow melt runoff to drain away from, rather than toward the pile. Don’t locate the pile in a low area that may become inaccessible due to mud or ponded water.
Well
Locate the pile away from wells to minimize seepage contamination. The pile should be at least 100 feet away and downslope from the well. This distance may increase on more permeable soils (sand, gravel, karst bed rock), or with shallow well depth. Separation of silage storages from a well are discussed “Water well, reservoir and spring location: A fact sheet for drillers and pump installers.”
Surface Water Resources
Silage leachate and runoff can contaminate surface water resources. Locate the silage pile as far as possible from concentrated flow patterns and surface waters.
Snow
Consider snow drift patterns. Don’t locate a pile where snow drift might restrict access.
Feeding
Consider how you will move the silage to the cattle or feeding system. If you will load silage directly into a TMR or other wagon, account for the area required to move the equipment to and from the pile. While a feed gate or electric-wire may be used to feed from the pile, we don’t recommend self-feeding directly from the pile due to excessive feeding losses.
Silo Refilling
Refilling a tower silo from a pile is an option for feeding systems not equipped to handle silage directly from a pile. For quickest refilling, site the pile so you can efficiently move the silage to the tower silo. Refill the silo when the weather is cool and fill as rapidly as possible. See “Transferring Silage Between Silos.” Size the pile based on tower silo capacity (Table 3).
Maneuvering Space
Don’t underestimate the space necessary to move equipment on and around the silage pile. If you ignore space requirements before construction, you may find it difficult to properly build, compact and remove silage from the pile.
Fencing and Wild Animals
Fence livestock away from the silage pile. Animals can damage the plastic cover, exposing the silage to air causing spoilage.
Rodents, squirrels, birds and other small animals will make holes in the plastic to seek food and shelter. Deer, foxes and other animals walking on a pile will punch holes in the plastic cover. Locate a silage pile away from woods, trash piles and other possible shelters. Provide a buffer zone of gravel around the pile to discourage rodents from accessing the pile. Keep weeds and grass cut or killed around the pile to reduce wild animal shelter. Establish a rodent control program. An electric fence around the pile may be necessary to restrict deer and cattle access. Inspect the plastic cover frequently (weekly in summer and biweekly in winter), and immediately repair holes to minimize spoilage losses. Use tape specifically designed to repair holes in plastic.
Site Preparation
Equipment traffic is high when feeding from the pile. Feed-out equipment often causes ruts and mud holes on unprepared sites. An improved surface allows all-weather access to the pile. Rain and silage seepage can make pile access difficult on unimproved ground. If you wait until the ground is frozen before feeding from the pile, remember the ground under the pile will not freeze and may become a problem. If possible, build a pile on a concrete or asphalt slab. The next best alternative is to construct a macadam surface (see “Using All-Weather Geotextile Lanes and Pads”).
One important design criteria is to construct the pad above existing ground level to allow rainfall and silage seepage to drain quickly from the pile. A 2% slope for the pad is required to encourage water runoff.
Pile Sizing and Construction
Size the pile so you remove at least six inches of silage from the face of the pile each day. Sizing for 12 inches per day is even better. This helps to minimize spoilage due to exposure to air. To properly size the pile, follow this step-by-step procedure:
- Determine the number of pounds of silage to be fed from the pile each day. For example, assume 4,000 lbs As Fed/day.
- Divide the weight fed by 40 lbs AF/ft3. In our example, 4,000 lbs AF/day divided by 40 lbs AF/ft3 = 100 ft3/day. This is the volume of silage removed from the pile each day.
- Assume a Daily Removal Rate (DRR) from the face of the pile. Use 1 ft/day for our example.
- Divide the volume removed (Step 2) by the Daily Removal Rate (Step 3). This is the cross section Area of the pile feeding face:
(Volume/day(ft3/day)) ÷ (Daily Removal Rate(ft/day)) = Feeding Face Area (sq ft)
(100 ft3/day) ÷ 1.0 ft/day = 100 sq ft - Assume an Average Pile Height (APH). The actual peak height will be more than the Average Pile Height due to pile top rounding. For our example, we will use an APH of 5 ft.
- Pile side slopes should be 3 horizontal to 1 vertical (Figure 1) so the sides can be driven on safely and plastic weighting will stay on the slope and hold the plastic tightly to the silage. The Top Width (TW) is the distance between each side slope at the Average Pile Height.
- Using the 3:1 side slope, The T op Width can be calculated by this equation:
Top Width = (Feeding Face Area/APH) – 3*APH - Using a 3:1 side slope, the Pile Bottom Width is calculated as:
Bottom Width = 6*APH + TW - The Bottom Length (BL) of the silage pile is calculated using this equation when the slope on each end is 3:1:
Bottom Length = FP * DRR + APH*3
FP = Feeding Period (days) over which the pile will be fed out
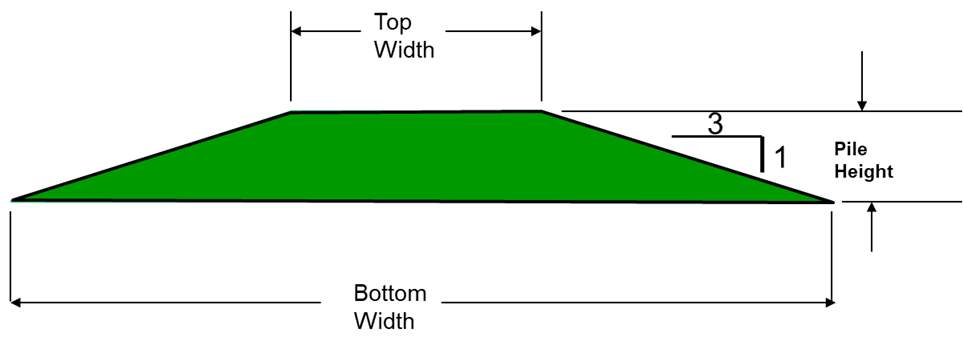
For our example, the pile has an Average Pile Height of 5 feet and using the equation of Step 7 a Top Width of 5 ft is calculated ((100 ft / 5 ft) – 3*5 ft). Using Step 8, the Bottom Width is 35 feet (6*5 ft + 5 ft). These are reasonable values, but if your calculations produce a Top Width less than zero, assume a shorter Average Pile Height and return to Step 7.
If this is still unrealistic, assume a smaller face removal rate (not less than 6 inches/day) and return to Step 4.
If you plan to feed from the pile for 200 days (FP), and the slope of silage on each end is 3:1, using the equation of Step 9, the Bottom Length in our example is:
BL = 200 days * 1 ft/day + 5 ft * 3 = 215 ft.
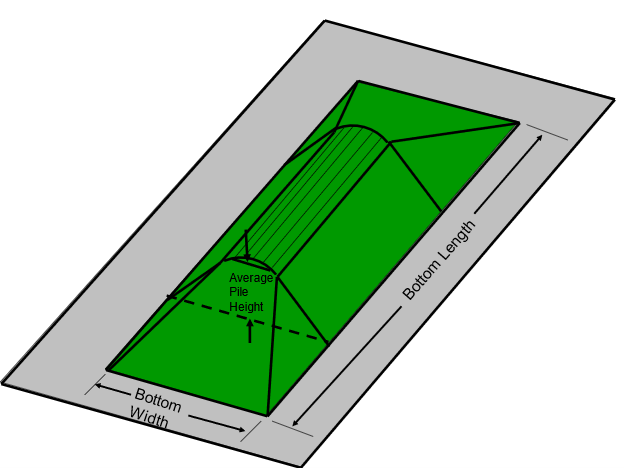
Tables 1 and 2 (below) show the silage needed and pile dimensions for various herd sizes, depending on the amount of silage dry matter fed per day per animal.
Similar calculations can be performed using the “Silage Pile Sizing Calculator” spreadsheet.
When your plans are to refill a tower silo from a silage pile, size the pile based on the capacity of the tower silo so the pile is emptied completely. The capacity of the tower silo can be determined from the “Tower Silo Capacity” spreadsheet.
The size of the pile can be determined using the “Silage Pile Capacity and Capital Cost Calculator” spreadsheet or by using the equations in steps 1-9 above. Table 3 gives some examples of pile sizes needed to fill given sized tower silos.
Table 1
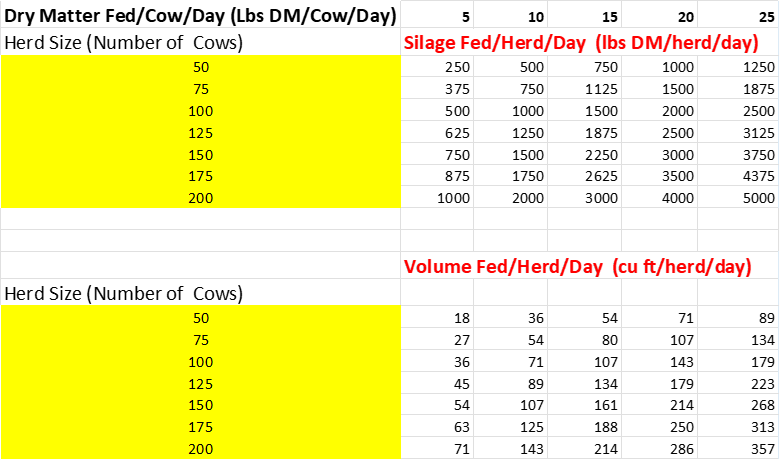
1Silage density of 14 lbs DM/ft3
Table 2
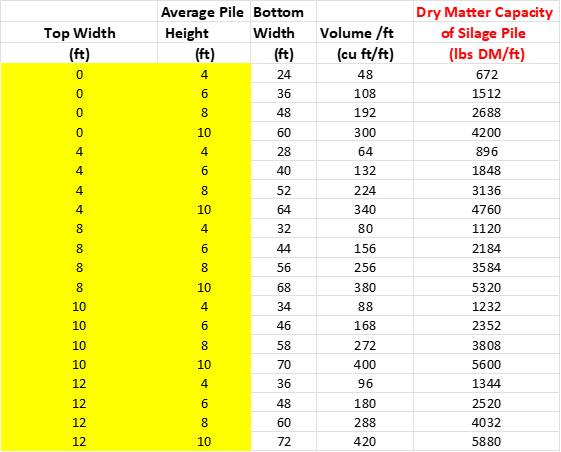
2Assumes side slopes of 3 horizontal to 1 vertical, silage density of 14 lbs DM/ft3
Table 3
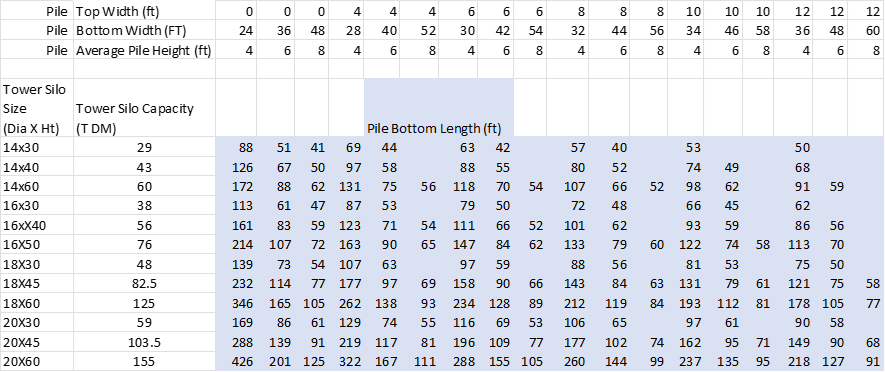
3Assumes Filling, Back and Side slopes of 3 horizontal to 1 vertical, pile silage density of 14 lbs DM/ft3, 10% dry matter loss while moving silage from pile silo to tower silo.
Pile Filling
Piles are generally filled with a tractor with a blade or front-end loader. The heavier the tractor the higher the likelihood of achieving high silage density.
To achieve high forage density, several packing tractor passes should be made over the same area. This is usually accomplished by driving along the length of the pile with adjacent tire passes. Driving across the pile (perpendicular to previous passes) can help to increase the uniformity of packing.
Filling and packing with the same tractor is limited to a relatively slow delivery rate of forage from the field. When high capacity forage harvesters are used, one tractor may be required for filling only and one or more tractors may be needed to pack the forage to achieve the desired forage density. Use the “Silage Pile Density Calculator” spreadsheet to help decide how many packing tractors are needed in your situation.
Within Figure 4 in the article “Packing Bunkers and Piles to Maximize Forage Preservation”, the effect of packing tractor weight and number of packing tractors can be observed. To minimize dry matter loss, the silage porosity should be less than 0.4. With a harvest rate above 75 metric tons per hour, a single 9,072 kg (20,000 lb.) packing tractor cannot achieve a porosity of 0.4 (solid red diamond) when the silage dry matter content is 35%. Using a single 18,144 kg (40,000 lb.) tractor packing on the same silage results in a porosity of 0.4 only at a harvest rate of 75 metric tons/hr. (solid black square). It isn’t until two 18,144 kg (40,000 lb.) packing tractors are used is the desired 0.4 porosity achieved over the various harvest rates evaluated.
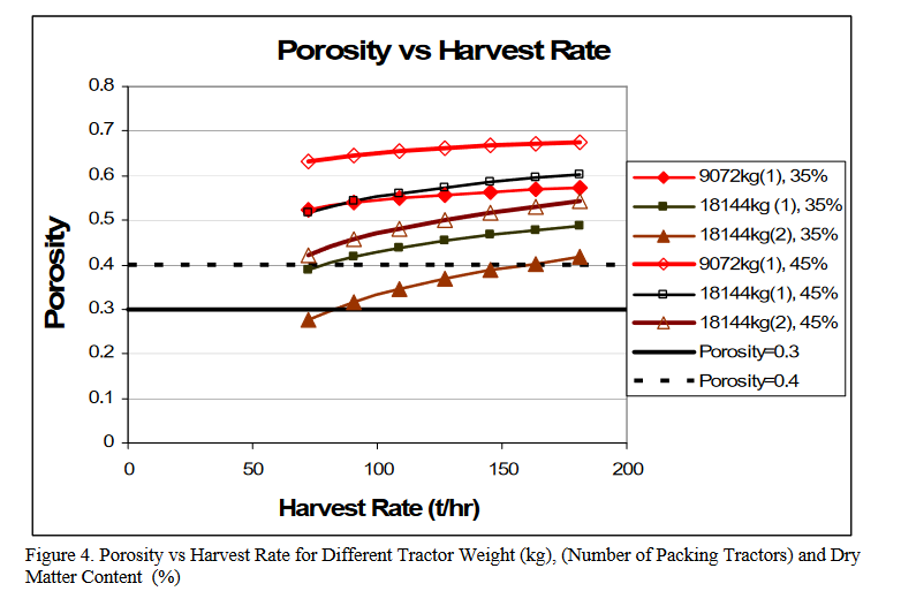
Two techniques are used for pushing the silage into the pile. In the most common method, the transport vehicle deposits the forage in front of the filling face and the filling tractor pushes the forage up the filling slope toward the back of the pile. In the second method, the transport vehicle deposits forage around the perimeter of the pile being filled and the filling tractor pushes forage up the filling slope toward the center. The second method allows more filling and packing tractors to be used safely on the pile. In both cases, the slope of the forage on the filling surface should be 3 or more units horizontal to 1 unit vertical. This slope is shallow enough to minimize the likelihood of tractor roll-over and allows most of the tractor weight to be exerted on the forage surface for optimum packing.
The thickness of the forage layer delivered in the filling process determines forage density after packing. Thinner layers of forage will be higher in density than thicker layers for the same number of packing passes. The recommended layer thickness of forage placed while filling is 6 inches or less.
Before applying the plastic cover, make several packing passes over the entire pile to achieve higher density in the top layer. This step is critical to reduce or eliminate silage spoilage directly under the plastic cover.
Covering the Pile
Immediately after completing the final packing passes, cover the pile with 6 mil polyethylene plastic. Thicker polyethylene plastic and or a layer of Oxygen barrier film under the 6 mil plastic provides better silage preservation. On large piles, multiple plastic sheets may be needed. Overlap these sheets by at least 4 feet and place the up-slope sheet over the down-slope sheet to shed water. Pay particularly close attention to weight the plastic or tarp well at the plastic joints.
When a pile is filled from one end to the other, the plastic cover can be installed on the back end once that end is filled. This can reduce exposure of that forage to oxygen as quickly as possible. If harvest is halted due to rainfall, covering the forage with plastic temporarily protects the top surface from moisture and oxygen infiltration which can cause spoilage in that layer.
The plastic should be pulled tightly and sealed along the sides by weighting with sand/pea gravel filled bags or piling a bead of limestone along the edge (Figure 3). Don’t use gravel or limestone screenings to seal the edge of the plastic as it likely will mix in with the silage. Feeding gravel or limestone screenings to the cattle may result in digestion system compaction. When held tightly against the pile, the plastic eliminates air spaces reducing spoilage. If using tires to hold the plastic down on top of the pile (see Figure 3) position the tires so they touch one another. This seals the plastic to the silage and minimizes air spaces.
Truck tire sidewalls are available for purchase and work better than whole car, truck or tractor tires. Tires are difficult to modify and whole tires are difficult to handle. If you are able to cut tires, cutting the tires in half along the circumference has several advantages. You’ll need half as many tires, they are lighter to handle, and rainwater drains more easily from the tires. If you use uncut tires, drill holes in the sidewalls to allow rainwater to drain – otherwise you could have a mosquito breeding area on your silage pile.
Plan an area to store the tires as they are removed from the pile during feed-out. If the tire storage area allows the tires to be positioned on edge or vertically, they can be loaded onto pallet forks by the operator eliminating loading labor.
Sand/pea gravel filled bags weighting a tarp (Figure 3) is an alternative to tires for holding the plastic next to the silage. Use a 10 ft x10 ft grid of sand/pea gravel filled bags to weight the tarp. Limit tarp size for more convenient removal when covered with snow and ice. If the plastic lifts or ripples in the wind, add additional weighting.
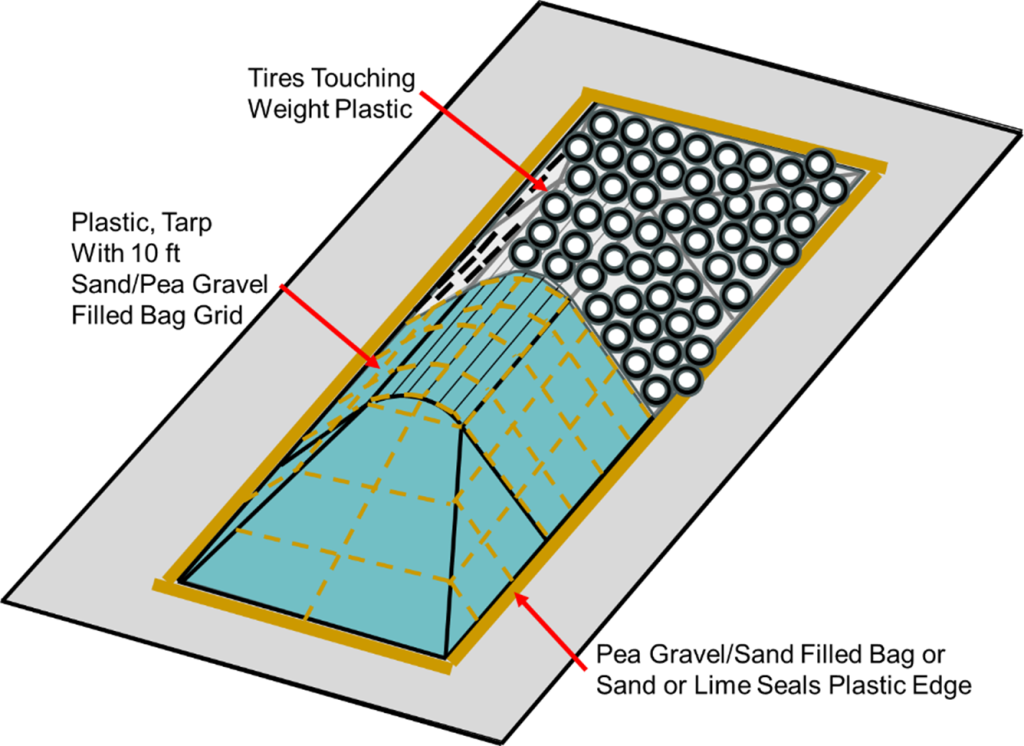
Forage Moisture
To increase packing effectiveness and improve fermentation, forage for silage piles should be slightly wetter than forage going into upright silos. Forage for top unloading upright silos typically contains 35 to 45 percent dry matter. Results from whole-plant corn silage moisture testing should be used to determine when the crop is ready for ensiling.
For corn silage piles, 30 to 35 percent dry matter promotes good packing, sealing and fermentation. When moving this higher moisture silage to a tower silo, expect dry matter losses due to leachate from the tower silo.
Alfalfa should be placed in a silage pile between 35-40 percent dry matter. Dry matter below 35 percent increases the likelihood of butyric acid production in Alfalfa silage.
Feed-out Practices
Dry matter losses at feed-out can be significant if good management practices are not observed. Remove only as much plastic cover as is needed to expose one day’s silage removal. To keep air from entering under the cut edge of the plastic, uniformly weight that edge with the pile weighting material. Remove and dispose of spoiled silage from the top of the pile.
During feed-out, leave a smooth tight feed-out face. A facing machine leaves a smoother face than a front-end loader or a silage rake. Remove only as much silage as will be fed in one day. Any excess silage should be accumulated in a pile on the floor and covered with weighted plastic to limit oxygen infiltration.
Summary
Properly constructed, a drive-over silage pile can provide efficient and economical silage storage. Proper design, filling, covering and feed-out is critical for optimizing silage dry matter recovery from a drive-over pile.
References
Barnett, K. and B. J. Holmes (2015). Silage Pile Sizing Calculator https://fyi.extension.wisc.edu/forage/files/2020/01/Silage_Pile_Sizing-English-Spanish-Portuguese-French-Protected.xlsx
Beef Housing and Equipment Handbook, MWPS #6. (1987) Midwest Plan Service. Iowa State University, Ames, IA 50011.
https://store.extension.iastate.edu/Product/2691
Clark, J. (2000). Storing Forage in Piles. University of Wisconsin Team Forage. Focus on Forage. Vol 2 No 5.
https://fyi.extension.wisc.edu/forage/storing-forage-in-piles/
Holmes, B. J. (2011). Silage Pile Capacity and Capital Cost Calculator.
https://fyi.extension.wisc.edu/forage/files/2014/02/Pile_Capacity2-23-12.xls
Holmes, B. et al. (2013). Dairy Freestall Housing and Equipment (MWPS-7) Midwest Plan Service (MWPS). Iowa State University, Ames, IA 50011.
https://store.extension.iastate.edu/product/2692
Holmes, B. J. (2020). Silage Pile Density Calculator Spreadsheet
https://fyi.extension.wisc.edu/forage/files/2020/05/PileDensCalcwPOROSITY-Spanish-5-10-20.xlsx
Holmes, B. J. and G. Frank (2023). Tower Silo Capacity Calculator.
https://cropsandsoils.extension.wisc.edu/articles/tower-silo-capacity-spreadsheet/
Janni, K., T Funk, and B. J. Holmes. (1999). Using All-Weather Geotextile Lanes and Pads (AED-45) Midwest Plan Service (MWPS). Iowa State University, Ames, IA 50011. https://store.extension.iastate.edu/Product/775
Lawrence, J., B. Luck, B. Holmes, L. Ferretto, and R. Shaver. (2022). Corn Silage: From Seed to Feed. Hay and Forage Grower. W. D. Hoard and Sons, Inc.
https://hoards.com/article-31720-corn-silage-from-seed-to-feed-(silg).html
Shaver R. and Jim Leverich (1999). Transferring Silage Between Silos. University of Wisconsin Team Forage. Focus on Forage. Vol 1: No 7.
https://fyi.extension.wisc.edu/forage/transferring-silage-between-silos/
Authors
John M. Roach is a consultant and owner of Roach & Associates, LLC, a dairy management and engineering firm consulting for dairy operations in the Midwest.
Brian J. Holmes is Professor Emeritus, Department of Biological Systems Engineering, College of Agricultural and Life Sciences, University of Wisconsin-Madison.